How leveraging smart factories optimises products and operations for manufacturers
Mei Dent, Chief Product and Technology Officer, TeamViewer
Manufacturing processes and supply chains have become more complex over the past few years, making traditional methods insufficient to meet the demand for greater customisation and shorter production cycles.
Manufacturers feel pressured by rising labour and material costs to find more efficient ways to produce high-quality goods. Additionally, the increasing need to meet environmental regulations and sustainability goals pushes manufacturers to adopt greener practices. As global competition intensifies, manufacturers must find ways to innovate and stay agile to respond quickly to market changes.
Smart factories address these challenges by integrating advanced technologies to create a more responsive, efficient, and sustainable production environment.
By leveraging technologies like artificial intelligence (AI), machine learning (ML), and the Internet of Things (IoT) to deliver predictive analytics and big data, manufacturers can optimise processes, manage inventory in real time, streamline logistics, and improve factory management.
Smart factories collect, process, and use this data to gain valuable insights. Real-time production monitoring and closed-loop optimisations, along with collaboration between advanced robotics and humans, help create these transformations.
However, a significant challenge in smart factory implementation is the disconnect between IT professionals and plant managers, particularly regarding data collection, outcome creation, and data protection.
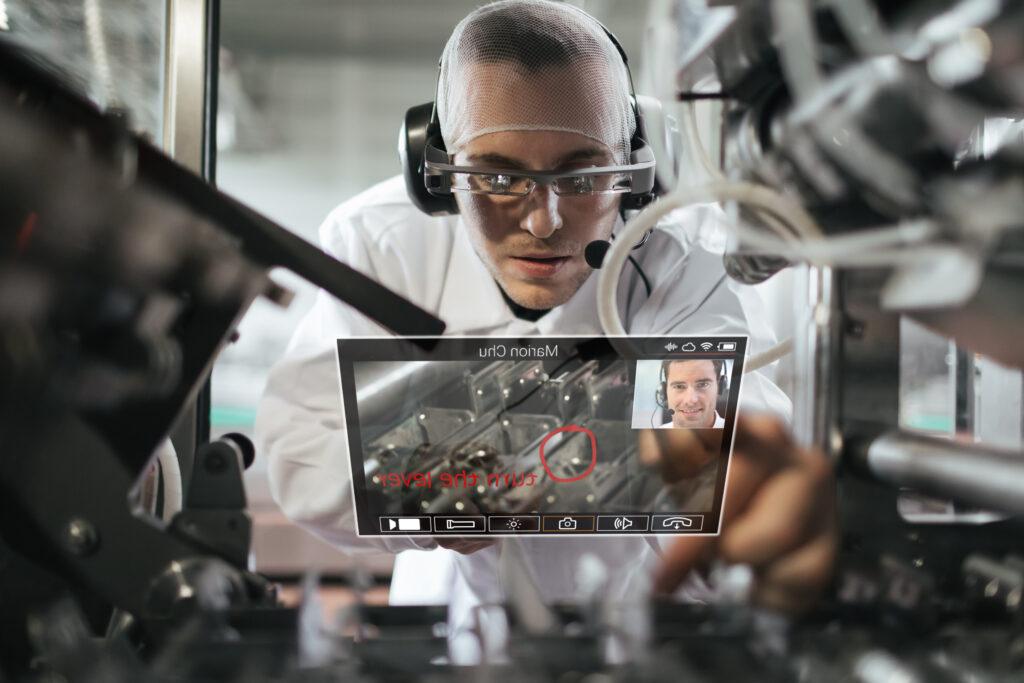
IT professionals often advocate for comprehensive data collection to optimise predictive maintenance, while plant managers are more concerned with the practical, immediate concerns such as knowing which machines are currently in production, how production is running, and maintaining seamless operations.
IT professionals’ preference for leveraging cloud solutions can also clash with plant managers’ concerns about security and the usability of hyper-scale offerings. For example, IT professionals may push for automated updates and virtualisation, whereas plant managers worry about if production is operating at the level needed and the potential disruptions to long-established production systems.
Bridging these differing perspectives is crucial for achieving successful IT and operational technology (OT) convergence in smart factories.
Manufacturers can leverage the benefits of smart factory technologies fully by aligning the objectives and addressing the concerns of both IT professionals and plant managers. These benefits include:
- Enhanced productivity and efficiency
Manufacturers can significantly boost productivity and efficiency by using predictive analytics and big data insights.
This provides optimised processes and just-in-time inventory management, reducing downtime and improving operational flow.
For instance, remote connectivity solutions provide detailed views of all IT and OT hardware assets, helping manufacturers manage warranties, patch information, and potential security risks while troubleshooting issues remotely.
- Improved workplace safety
Smart factories create safer work environments by reducing the risk of injuries from harmful objects, heavy lifting, and repetitive tasks.
Advanced robotics and automated systems handle these dangerous jobs, ensuring worker safety. Additionally, industrial augmented reality (AR) solutions enhance frontline workers’ skills by providing step-by-step instructions and remote assistance, empowering them to perform complex tasks more efficiently.
- Optimised sustainability efforts
Real-time data helps manufacturers adopt sustainable practices by optimising energy consumption and reducing waste.
Consumers are increasingly willing to pay more for products made responsibly, making sustainability a competitive advantage. Implementing a central industrial IoT platform facilitates seamless communication between machines and IT systems across multiple factory sites, creating a strong foundation for sustainable operations.
- Upgraded product quality
Manufacturers can respond to trends and customer demands quickly by integrating cloud connectivity and real-time insights into the manufacturing process.
This leads to higher product quality and a better customer experience as companies can deliver customised and up-to-date products. Advanced platforms structure and analyse manufacturing data, turning it into a powerful foundation for AI-driven insights, which allows manufacturers to make informed, data-driven decisions and maintain an updated view of production.
- Streamlined logistics and material flow
Automated material handling systems streamline logistics and material flow within the factory, minimising manual handling and reducing cycle times.
Leading manufacturers’ smart factories interconnect humans, robots, and logistics using digital twin technology—a virtual representation of a physical object, process, or service—and AI-driven systems to optimise production plans and inventory management. This ensures high efficiency and responsiveness to customer demands.
Facilitating IT and OT convergence
A successful smart factory relies on the seamless convergence of IT and OT. Although they have different focuses—IT on data processing and communication, and OT on monitoring and controlling physical devices—both domains must work together to fully realise smart factory innovation’s benefits. There are four critical steps to facilitate this convergence:
- Finding common ground
IT and OT need to understand each other’s priorities and challenges to collaborate effectively. IT professionals should spend time on the plant floor to gain insights into daily operations and manufacturing practicalities.
- Practical solutions
IT professionals should use practical, easy-to-understand language when communicating with plant managers, avoiding technical jargon and buzzwords. Solutions should be user-friendly and easily comprehensible by operators, not just IT administrators.
- Leveraging private cloud and edge architectures
Manufacturers can adopt private cloud and edge architectures to balance data processing needs and security concerns. These technologies offer scalable solutions that meet the plant’s real-time demands while ensuring robust data protection.
- Establishing joint KPIs
To measure smart factories’ success, IT and OT departments must agree on common key performance indicators (KPIs) across productivity, timeliness, quality, resilience, innovation, and costs. Aligning these metrics ensures both teams work towards shared goals and enhances overall factory performance.
While the scope of smart factory applications is broad, it is important to note that most vendors focus on specific areas and the industry is still learning to find the best ways forward.
Current use cases in smart factories might be limited; however, there are significant strengths in areas such as warehouse picking and after-sales services, like remote support and training, where innovation and value delivery are well-positioned to drive progress.
Embracing smart factory innovation puts manufacturers at the cutting-edge of industrial progress, unlocking impressive improvements in productivity, efficiency, safety, sustainability, and product quality.
By seamlessly merging IT and OT, companies can break down barriers and adopt practical, data-driven solutions that optimise operations and build resilience. Leveraging real-time data, predictive analytics, and advanced automation, manufacturers can quickly adapt to market demands, minimise downtime through predictive maintenance, and boost sustainability by reducing waste and optimising energy usage.